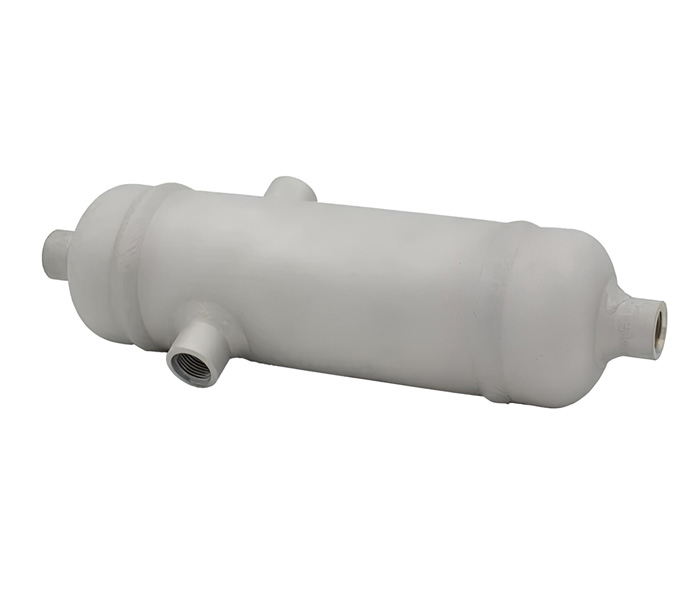
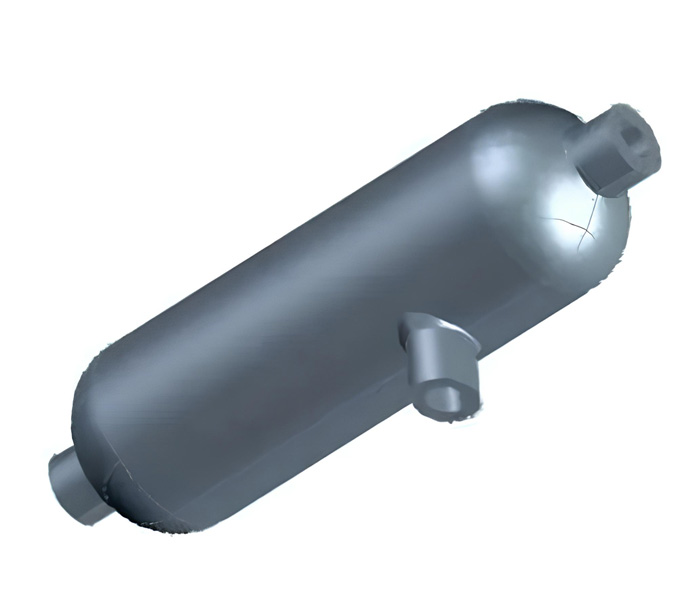
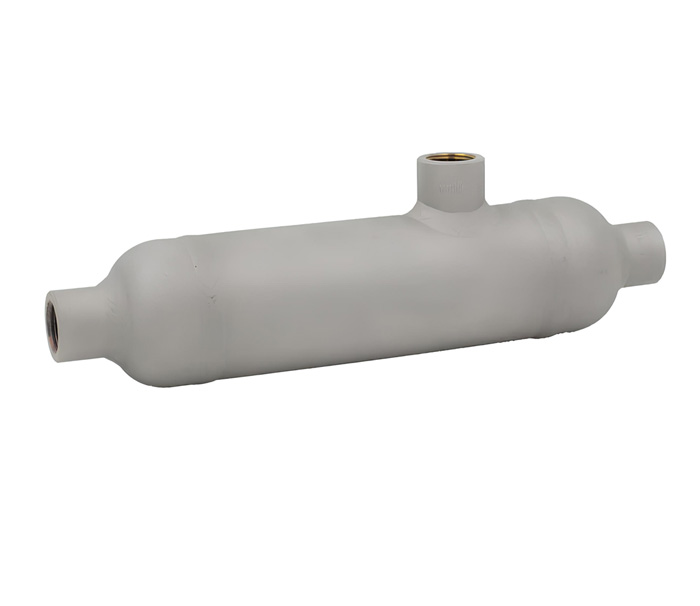
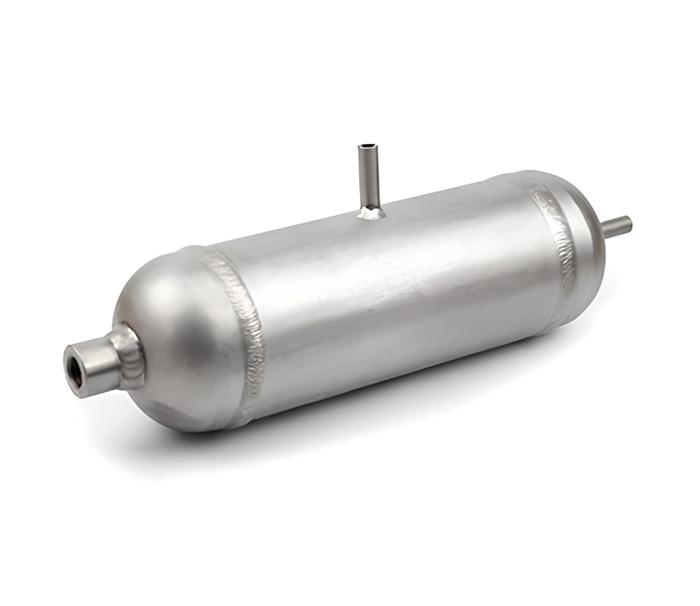
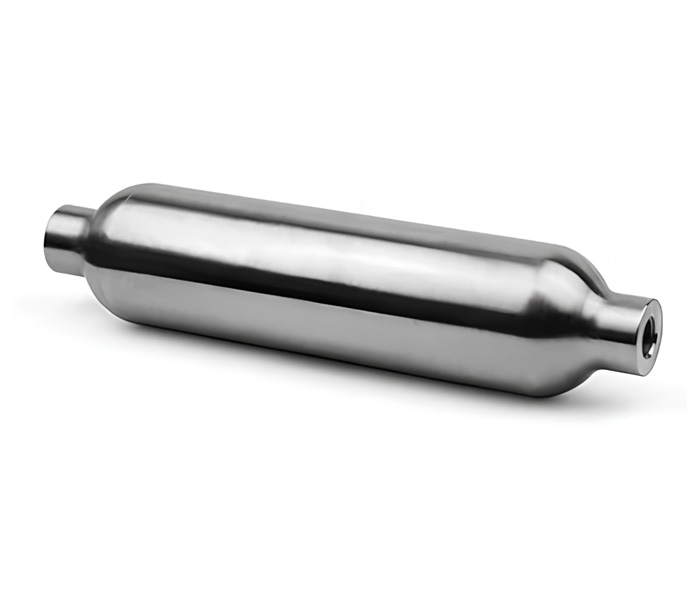
What is Condensate Dampening Pot?
A condensate dampening pot is a component used in steam and condensate systems to address the issue of water hammer, especially when condensate needs to be lifted to higher elevations in pipelines. Water hammer occurs when there is a sudden stop or change in the direction of fluid flow, causing a shockwave within the piping system.
The condensate dampening pot is typically installed at the lowest point of the pipeline, and its purpose is to provide a cushioning effect to neutralize the effects of water hammer. It acts as a buffer or shock absorber, helping to absorb the energy generated during the sudden changes in fluid flow, thereby preventing the damaging impact of water hammer on the pipeline components.
In addition to mitigating water hammer, the condensate dampening pot allows condensate to be discharged without generating noise. This is important in maintaining a quiet and safe operation of the steam and condensate system, especially in industrial settings where excessive noise can be a concern.
The design of the condensate dampening pot involves creating a chamber or reservoir that accommodates the condensate, allowing for a smoother and controlled discharge without the disruptive effects associated with water hammer. This contributes to the overall efficiency and safety of steam and condensate systems in various industrial applications.
Arrotop’s Condensate Dampening Pots offer a reliable solution to prevent water hammer and ensure safe condensate discharge in steam systems. Their robust construction, ease of installation, and wide range of applications make them an essential component for maintaining system integrity and efficiency.
Product Data
The Condensate Dampening Pot by Arrotop is an essential component in steam and condensate systems. It is designed to mitigate the damaging effects of water hammer, which can occur when condensate is lifted to higher elevations in pipelines. This device ensures the safe and noise-free discharge of condensate, protecting pipeline components and maintaining system integrity.
In steam and condensate systems, there is a common need to elevate condensate to higher pipelines, such as those serving heat exchangers positioned at a lower level than the main condensate line. This elevation process may result in water hammer, potentially causing damage to pipeline components within your steam system and posing safety risks to your personnel.
It imparts a damping effect to counteract water hammer and facilitates noise-free discharge of condensate.
Features
- Water Hammer Mitigation: Neutralizes water hammer by providing a cushioning effect, protecting pipeline and other components from damage.
- Noise-Free Discharge: Ensures condensate is discharged without noise, enhancing operational comfort.
- Safety Improvement: Prevents damage to pipelines and enhances system safety.
- Easy Installation: Designed for installation at the lowest point of the pipeline, simplifying the setup process.
- Maintenance Reduction: Reduces the need for frequent maintenance by preventing damage to system components.
- Versatility: Suitable for a variety of industrial applications, including high-pressure and high-temperature environments.
Technical Specifications
- Sizes: Available from ½” to 4”.
- Working Pressure: PN 16 and PN 40
- Materials: Stainless Steel: SS 304/L, SS 316/L, Carbon Steel, Duplex Stainless Steel, Super Duplex Stainless Steel, Alloy Steel, Other materials available on request
Technical Data
- Design Temperature: Up to 800°F (427°C)
- Design Pressure: Up to 6000 psi (410 bar)
- Compliance: ASME, API, ISO standards
Condensate Dampening Pot functions
- Rising condensate lines might experience water hammer due to steam bubbles carried over or generated from flashing.
- If these steam bubbles enter segments of the line with condensate at significantly lower temperatures, water hammer may occur.
- The steam bubbles rapidly collapse and significantly decrease in volume as they transition into liquid form. This creates a vacuum that is swiftly filled by inflowing condensate, triggering water hammer.
- The pot is positioned at the pipeline’s lowest point, where it takes in condensate and serves as a buffer to mitigate water hammer.
- The condensate inlet and outlet are positioned to create a cushion for dampening, comprising air and steam bubbles, which forms in the upper section of the pot during plant startup. In the lower part of the pot, condensate remains, serving as a sealing fluid. Pressure within the pot drives the flowing condensate onward into the higher condensate main.
Material
- Flange : Steel – 1.0460 (P250GH+N), Stainless Steel – 1.4571 X6CrNiMoTi17-12-2)
- Base : Steel – 1.0425 (P265GH), Stainless Steel – 1.4571 X6CrNiMoTi17-12-2)
- Pipe (jacket) : Steel – 1.0345 (P235GH+N), Stainless Steel – 1.4571 X6CrNiMoTi17-12-2)
- Pipe (Standpipe) : Steel – 1.0345 (P235GH+N), Stainless Steel – 1.4571 X6CrNiMoTi17-12-2)
- Pipe (foot) : Steel – 1.0345 (P235GH+N), Stainless Steel – 1.4571 X6CrNiMoTi17-12-2)
Model Numbers
Model Number | Material | Size Range |
---|---|---|
ARO-CDP-304-001 | Stainless Steel 304/L | ½” to 4″ |
ARO-CDP-316-002 | Stainless Steel 316/L | ½” to 4″ |
ARO-CDP-CS-003 | Carbon Steel | ½” to 4″ |
ARO-CDP-DSS-004 | Duplex Stainless Steel | ½” to 4″ |
ARO-CDP-SDSS-005 | Super Duplex Stainless Steel | ½” to 4″ |
ARO-CDP-AS-006 | Alloy Steel | ½” to 4″ |
ARO-CDP-OMR-007 | Other Materials on Request | ½” to 4″ |
Dimensional Data
Size | Length (mm) | Width (mm) | Height (mm) |
---|---|---|---|
½” | 150 | 60 | 100 |
1″ | 200 | 80 | 150 |
2″ | 250 | 100 | 200 |
4″ | 300 | 150 | 250 |
Applications of Condensate Dampening Pot
- Heat Exchangers: In systems where condensate needs to be lifted to reach heat exchangers positioned at higher elevations, condensate dampening pots are employed to prevent water hammer and ensure a controlled discharge.
- Industrial Processes: Various industrial processes, such as those in chemical plants, refineries, and manufacturing facilities, may involve steam and condensate systems where condensate dampening pots are used to protect equipment and maintain system efficiency.
- Power Plants: Condensate dampening pots are utilized in power generation facilities to address water hammer issues in steam and condensate systems, particularly when condensate is lifted to higher levels within the plant.
- HVAC Systems: Heating, ventilation, and air conditioning (HVAC) systems often incorporate condensate dampening pots to control the discharge of condensate and prevent water hammer in pipes.
- Textile Industry: In textile manufacturing, where steam is commonly used for processes like dyeing and finishing, condensate dampening pots help maintain system integrity and prevent damage to components.
- Paper Mills: Paper and pulp manufacturing processes involve steam and condensate systems, and condensate dampening pots contribute to the protection of equipment and the smooth operation of these systems.
- Pharmaceutical Production: Steam and condensate systems in pharmaceutical facilities benefit from condensate dampening pots to ensure the controlled discharge of condensate and prevent water hammer-related issues.
- Food and Beverage Processing: Condensate dampening pots are employed in the food and beverage industry to maintain the efficiency of steam and condensate systems during various production processes.
- Chemical Processing Plants: In chemical processing industries, where precise control of fluid flow and the protection of equipment are crucial, condensate dampening pots are used to address water hammer challenges.
- Mining Operations: Mining facilities that utilize steam for various processes may incorporate condensate dampening pots to safeguard equipment and prevent disruptions caused by water hammer.
Advantages of Condensate Dampening Pot
- Water Hammer Mitigation: The primary advantage is the ability to effectively mitigate water hammer, preventing the damaging shockwaves that can occur during abrupt changes in fluid flow.
- Protection of Pipeline Components: By providing a cushioning effect, condensate dampening pots help protect pipeline components, such as valves, pumps, and other equipment, from the potentially harmful impacts of water hammer.
- Reduced Noise Levels: Condensate dampening pots contribute to a quieter operation by allowing condensate discharge without the generation of noise. This is especially important in environments where noise control is a consideration.
- Enhanced System Safety: The damping effect not only protects equipment but also contributes to the overall safety of the steam and condensate system by minimizing the risk of damage and potential safety hazards.
- Smooth Condensate Discharge: The design of the dampening pot allows for a controlled and steady discharge of condensate, promoting smooth and efficient operation within the steam and condensate system.
- Extended Equipment Lifespan: By reducing the impact of water hammer on pipeline components, condensate dampening pots contribute to the extended lifespan of valves, pumps, and other system elements.
- Versatility in System Design: Condensate dampening pots can be strategically placed at the lowest points in the pipeline, offering flexibility in system design and ensuring effective water hammer protection where needed.
- Maintenance of Operational Efficiency: The mitigation of water hammer helps maintain the operational efficiency of steam and condensate systems, minimizing disruptions and the need for frequent maintenance.